- A +
- A
- A -
Blades are an important component of the turbine section of aircraft engines. The high-speed rotating blades are responsible for sucking high-temperature and high-pressure airflow into the burner to maintain the engine's operation. Metal fatigue of blades is the main cause of engine failure. Strong vibration or resonance may cause metal fatigue.
Physical picture of aircraft blades
1. Engine blades generally bear greater working stress and higher operating temperature, and stress and temperature changes are also more frequent and severe. In addition, there are corrosion and wear problems. The requirements for the working conditions are very demanding, so the blades are required to The processing accuracy is very high.
2. At the same time, in order to improve efficiency, the surface shape of aircraft blades is usually designed as a twisted variable-section curved surface with a complex shape. Therefore, the precise geometric shape of the blade has become a necessary prerequisite for turbine machining.
3. Three-dimensional measurement is required in a non-destructive manner for the airfoil cross-sectional area, alignment, blade profile, trailing edge radius and blade root shape, which is a challenge to traditional measurement methods.
Aircraft blade STL data chart
Equipment used: HOLON 3D handheld three-dimensional scanner Model 37
Model 37 adopts the latest handheld design, is lightweight and easy to carry; it has 22 laser lines + 1 beam for deep hole scanning + 14 beams for fine scanning, a total of 37 laser lines, and the three scanning modes can flexibly scan the variable cross-section and curved surfaces of blades;
The scanning speed is fast, the accuracy is high, and the stability is strong. Dual industrial cameras, automatic stitching technology of landmark points are used in conjunction with independently developed scanning software; ultra-high scanning accuracy and work efficiency, flexible and convenient operation;
Model 37 uses non-contact scanning, which can be used immediately to avoid damage to the blades to the greatest extent.
Comparative inspection and analysis chart of aircraft blades
Comparative inspection and analysis chart of aircraft blades
Comparative inspection and analysis chart of aircraft blades
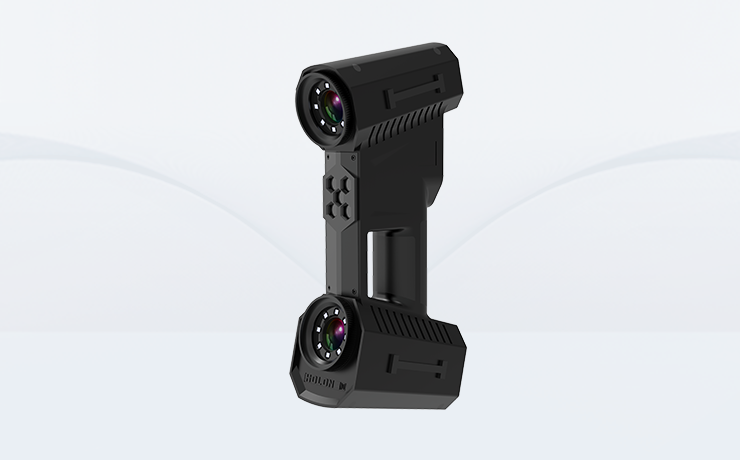
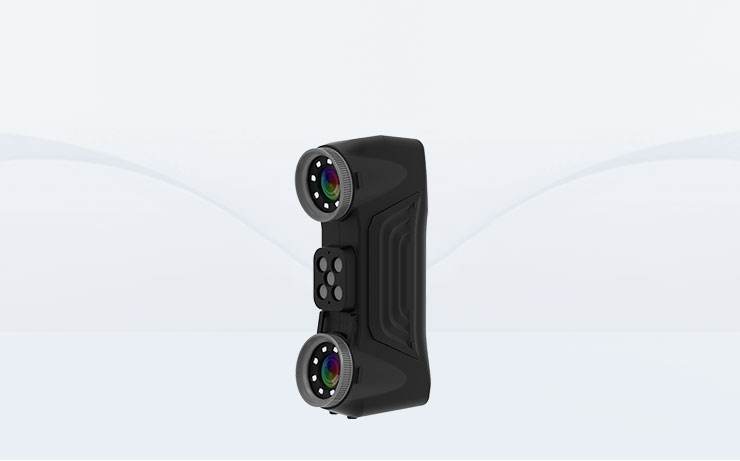
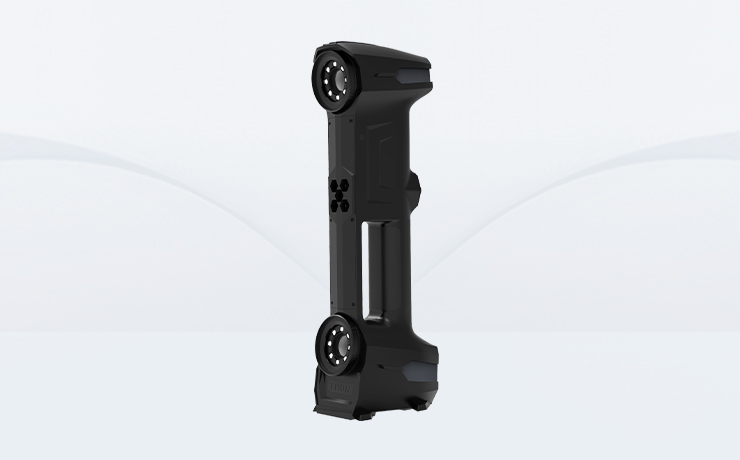