- A +
- A
- A -
The automated machine system brings great convenience. It is used in conjunction with robots for path planning. Good path planning is the key to the efficient operation of the robot production line. On the basis of predicting the robot's operating path, by establishing the robot's spatial coordinate system, Analyze the methods and influencing factors of the robot's initial pose and path selection. Check whether the robot path planning method meets actual production requirements.
Real photos of automated production lines
Because it is doing path planning, the system requirements for each link of the automated production line are very high. They can be used in conjunction with the robot to avoid errors. Therefore, the requirements for scanning and obtaining spatial coordinate data are very high. The traditional method of fixed scanning is not a very convenient scanning operation. The scanning process is difficult and time-consuming, and it is impossible to obtain effective coordinate information.
On-site scan of automated production line
After understanding and combining our past experience, we used our company's high-precision, fast scanning, and strong stability handheld 3D scanner Model 29. The handheld 3D scanner can be rotated at will to scan from different angles and positions, and multiple laser line modes can Switch to single laser scanning mode, which is suitable for scanning deep holes and dead corners. There is also fine mode, which can scan small features and greatly improve data accuracy. It is easy to use and easy to operate.
Automated production line STL data chart
Automated production line STL data chart
Import the scanned data into the 3D detection software for analysis and obtain a high-precision spatial coordinate data report. This solves the problems faced by customers in this regard, provides effective coordinate values, and is an important reference value in cooperating with robot design to speed up the project progress.
Automated production line STL data chart
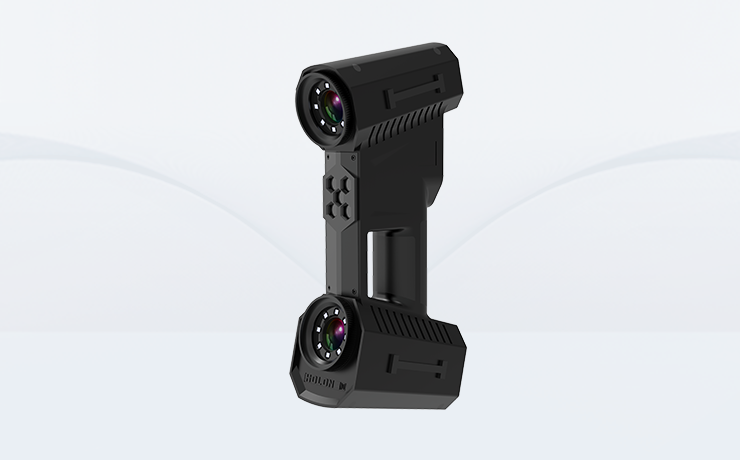
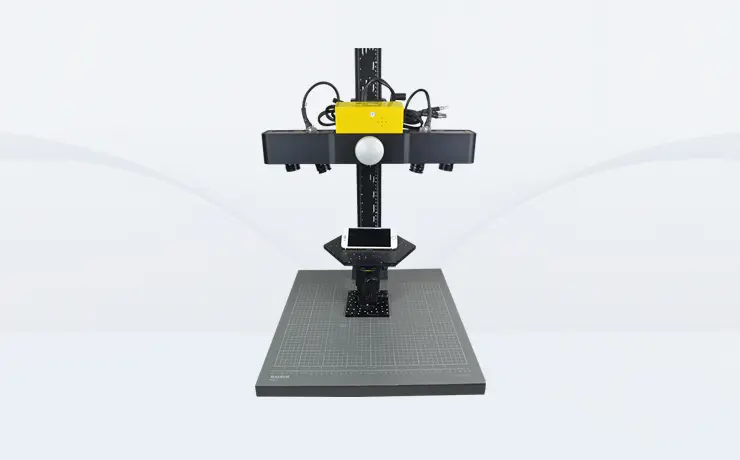
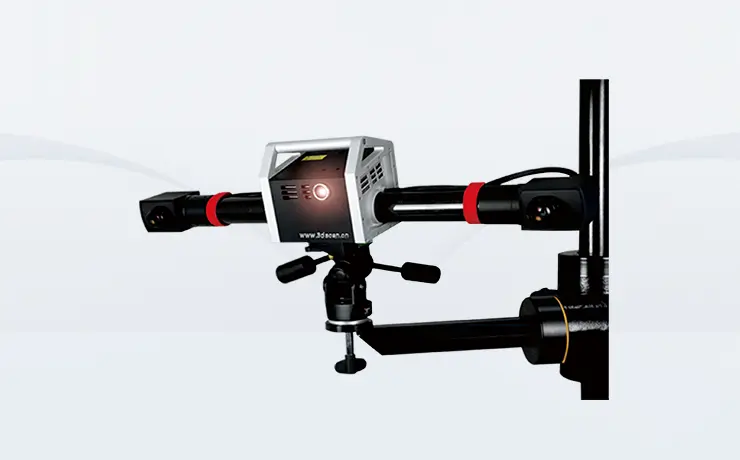