- A +
- A
- A -
Folding contact scanning
Contact 3D scanners calculate depth by actually touching the object surface, such as coordinate measuring machines, which are typical contact 3D scanners. This method is quite accurate and is often used in the engineering manufacturing industry. However, because it must contact the object during the scanning process, the object to be measured may be damaged by the probe, so it is not suitable for high-value objects such as ancient cultural relics and relics. reconstruction work.
In addition, contact scanning takes a longer time than other methods. Today's fastest coordinate measuring machines can complete hundreds of measurements per second, while optical technologies such as laser scanners operate at frequencies as high as 10,000 to 5 times per second. Millions of times. Non-contact active scanning Active scanning refers to projecting additional energy to objects and calculating three-dimensional spatial information through the reflection of energy. Commonly used projected energies include general visible light, high-energy beams, ultrasound and X-rays.
Folded time difference ranging
Time-of-flight ranging, or 'time-of-flight ranging' 3D laser scanner is an active scanner that uses laser light to detect targets. The LiDAR in the picture is a laser rangefinder with time difference ranging as its main technology. This laser rangefinder determines the distance from the instrument to the target surface by measuring the round-trip time of the laser pulse emitted by the instrument. That is, the instrument emits a laser light pulse. The laser light hits the surface of the object and is reflected. The detector in the instrument receives the signal and records the time.
Since the speed of light is a known condition, the time for one round trip of the optical signal can be converted into the distance traveled by the signal. This distance is twice the distance from the instrument to the object surface. Therefore, if let be the time for one round trip of the optical signal, Then the distance traveled by the optical signal is equal to. Obviously, the measurement accuracy of a time-lag 3D laser scanner is affected by how accurately we can measure time, because in about 3.3 picoseconds (picoseconds), the light signal travels 1 mm.
Folded triangulation
The triangulation ranging 3D laser scanner is also an active scanner that uses laser light to detect environmental conditions. Compared with the time-of-flight ranging method, the triangular ranging method 3D laser scanner emits a laser to the object to be measured, and uses a camera to find the laser spot on the object to be measured. As the distance of the object to be measured (distance triangulation ranging 3D laser scanner) is different, the position of the laser spot in the camera screen is also different. This technology is called triangular ranging because the laser spot, camera, and laser itself form a triangle.
The distance between the laser and the camera and the angle of the laser in the triangle are conditions we already know. Through the position of the laser spot in the camera frame, we can determine the angle of the camera in the triangle. These three conditions can determine a triangle and calculate the distance of the object to be measured. In many cases, people use linear laser stripes instead of single laser spots to scan the object to be measured, which greatly speeds up the entire measurement process.
The handheld laser scanner constructs 3D graphics through the above-mentioned triangular ranging method: through the handheld device, the object to be measured emits laser spots or linear laser light. Using two or more detectors (coupling components or position sensing components) to measure the distance from the surface of the object to be measured to the handheld laser product usually requires the use of a specific reference point - usually a sticky, reflective The patch is used to position and calibrate the scanner in space. The data obtained by these scanners will be imported into a computer and converted into a 3D model by software. Handheld laser scanners usually combine data obtained by passive scanning (visible light) (such as the structure and color distribution of the object to be measured) to construct a more complete 3D model of the object to be measured.
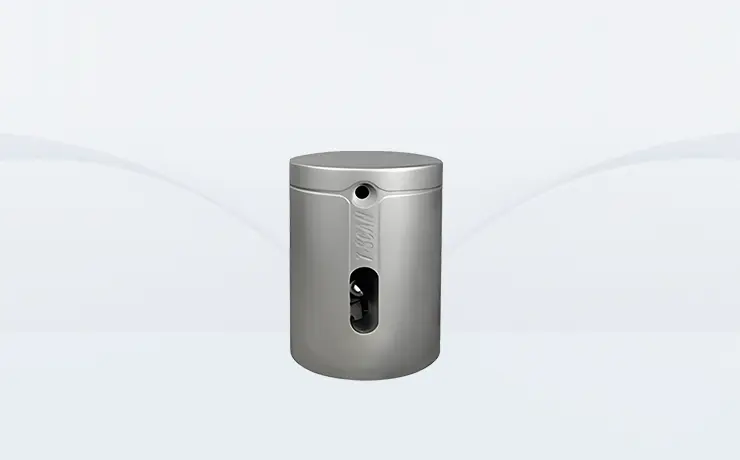
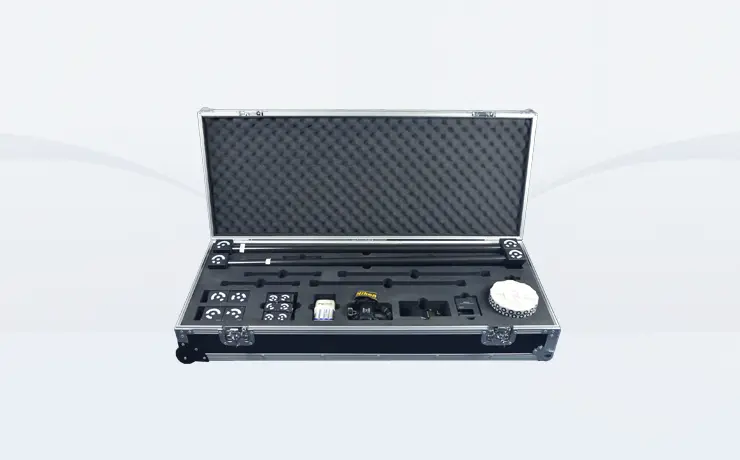
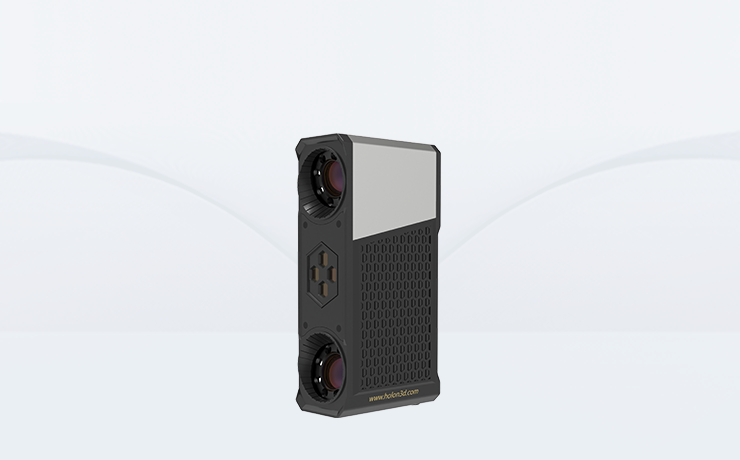