- A +
- A
- A -
Lufthansa's largest repair base in Asia adheres to rigorous work principles and needs to carry out three-dimensional reverse engineering of the aircraft engine air inlet cavity wall to obtain high-precision three-dimensional data for mold opening and processing to reduce the difficulty of later repair work.
1. The air inlet cavity wall of the aircraft engine is large, and the traditional measurement method is too inefficient and inaccurate, making it very difficult to reverse design and model in the later stage. Waste too much human and material resources.
2. The curvature of the outer surface of the aircraft engine air inlet cavity wall is difficult to measure through manual comparison. The customer requires that complete and accurate data be obtained in a short period of time so that follow-up work can be carried out quickly and ensure high quality service.
Customers hope to obtain complete and accurate three-dimensional data of the aircraft engine air inlet cavity wall in a short period of time. HOLON 3D proposes a solution based on the problems faced by customers: use the camera-type three-dimensional scanner HL-3DS+ to quickly and accurately The three-dimensional data of the engine air inlet cavity wall was obtained, the scanned 3D data was imported into the software to fit the SLT triangular mesh surface, and then imported into the three-dimensional design software for reverse design. The efficiency of product structure design and improvement was improved, follow-up work was carried out quickly, and the service project was completed within the specified time.
Aircraft engine air inlet cavity wall renderings
Site view of engine air inlet cavity wall
Aircraft engine air inlet cavity wall STL data diagram
Aircraft engine air inlet cavity wall STL data diagram
Aircraft engine air inlet cavity wall STL data diagram
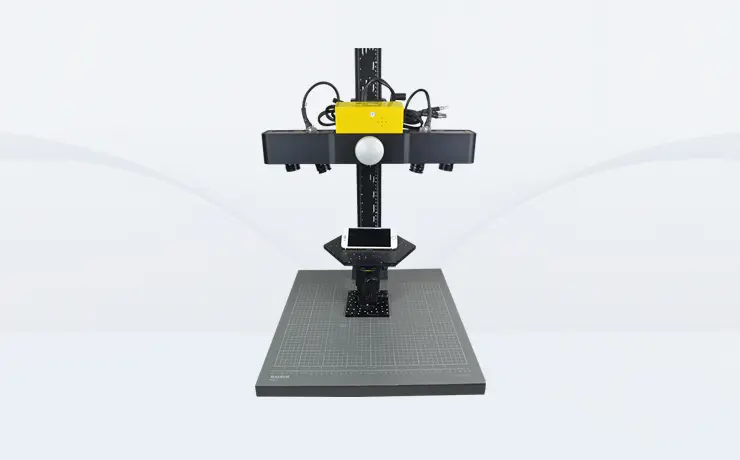
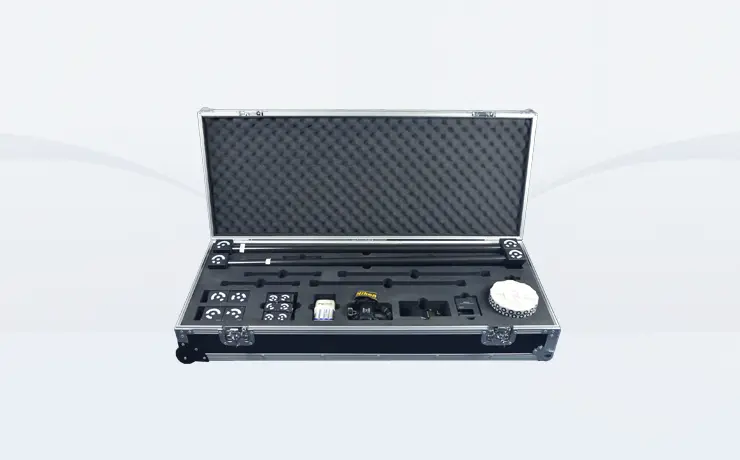
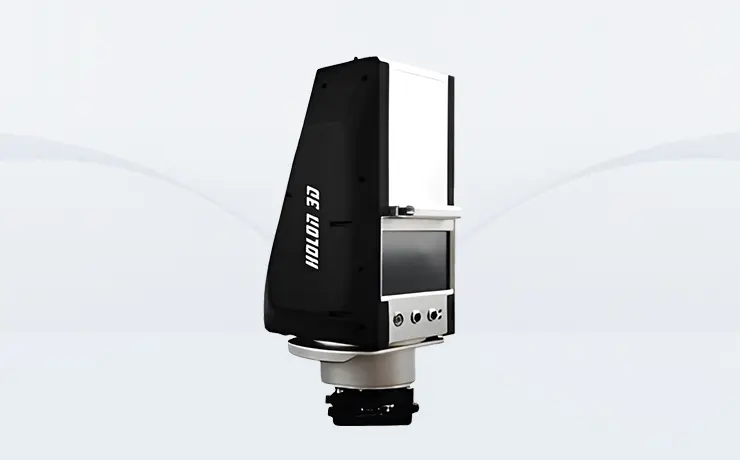